Technical Challenges: Engineering Accessible Agricultural Robotics
June 6, 2025
The agricultural sector stands at the cusp of a significant transformation, driven by the increasing need for efficiency, sustainability, and precision. Robotics offers a compelling solution, yet the widespread adoption of advanced autonomous systems has historically been constrained by high capital expenditure and the perceived fragility of complex machinery in demanding outdoor environments. At Spring Agriculture, our engineering philosophy addresses this directly: we design robots that are not only robust and reliable but also remarkably cost-effective, making advanced automation accessible to a broader range of farming operations.
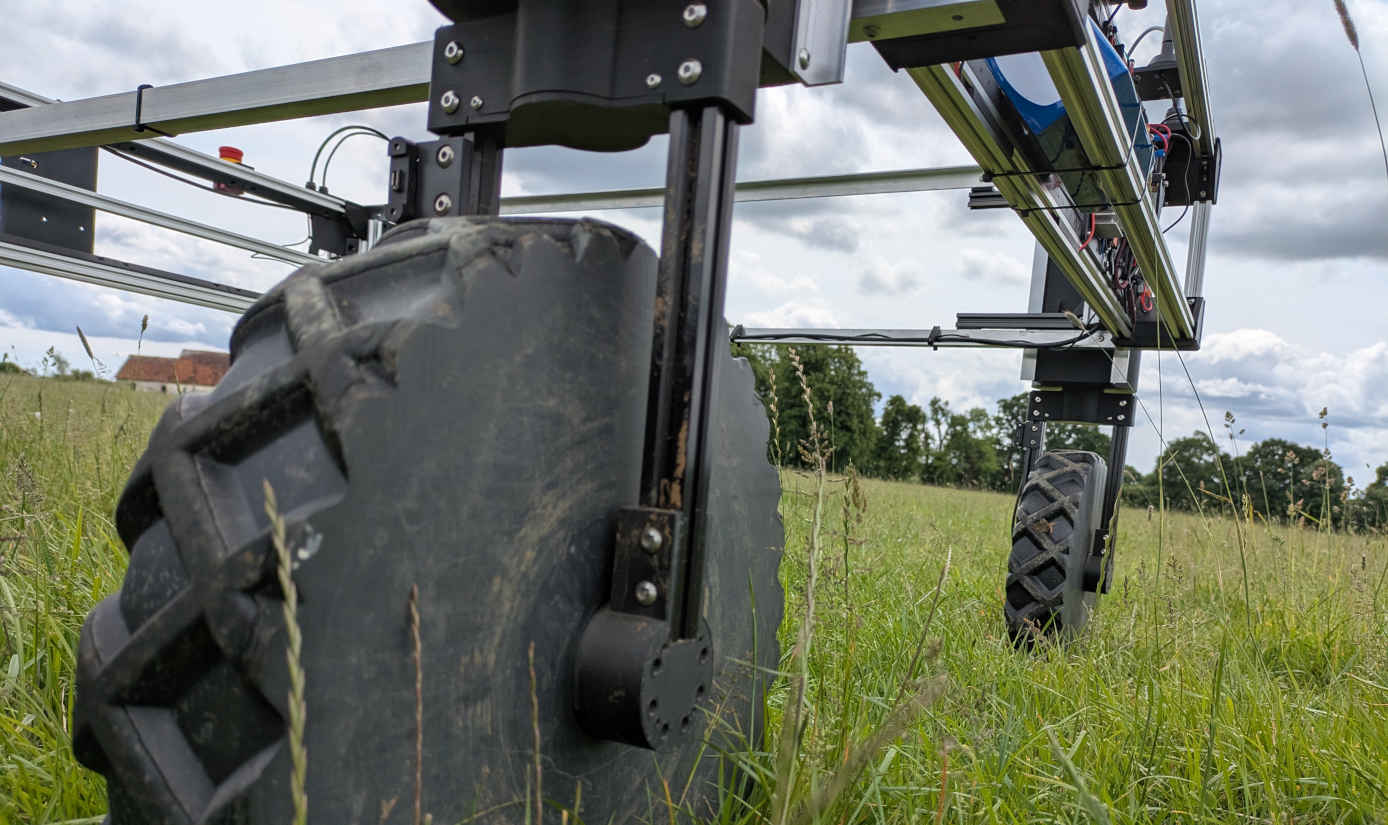
Our approach centers on a hybrid mechanical design that intelligently combines readily available, high-strength aluminum extrusion profiles with custom-fabricated components produced through Fused Filament Fabrication (FFF) 3D printing. The extrusion profiles form the foundational skeletal structure of our robots, providing inherent rigidity and a modular framework that is both strong and easily reconfigurable. This allows for rapid assembly and modification, leveraging the established benefits of industrial aluminum profiles. Complementing this, FFF 3D printing enables us to produce a vast array of bespoke parts: custom brackets, sensor mounts, protective enclosures, and even functional mechanical elements such as gears, pulleys, and specialized linkages. This combination allows us to tailor specific geometries and functionalities without resorting to expensive, time-consuming traditional machining or injection molding.
"Our hybrid mechanical design combines industrial aluminum with flexible 3D printing, enabling rapid iteration and strong, economical solutions."
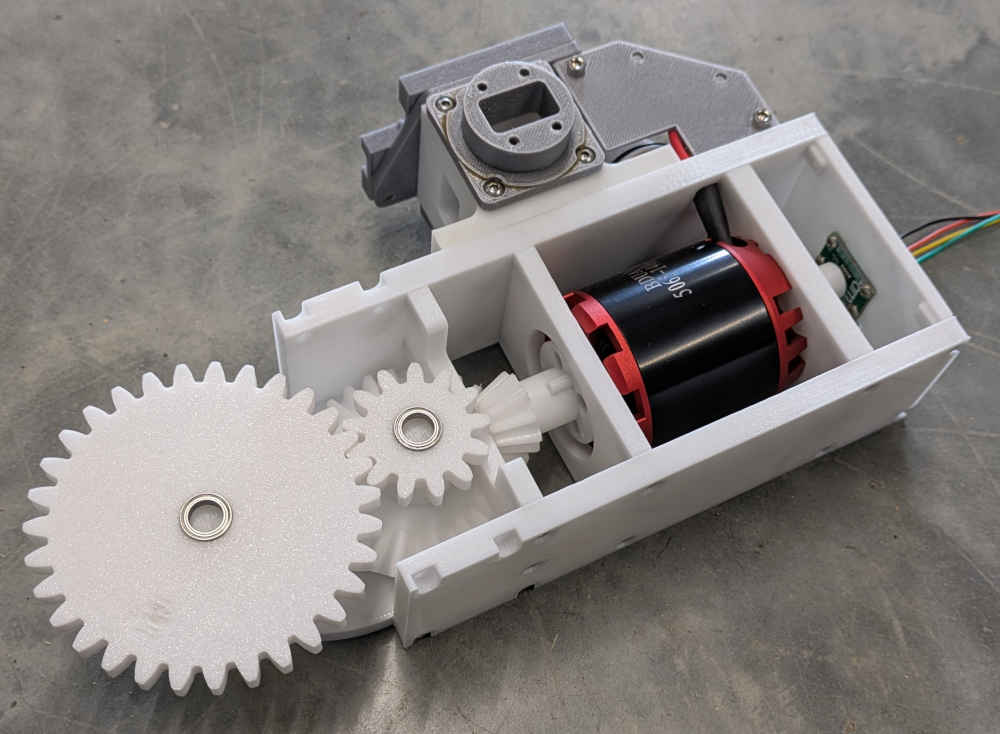
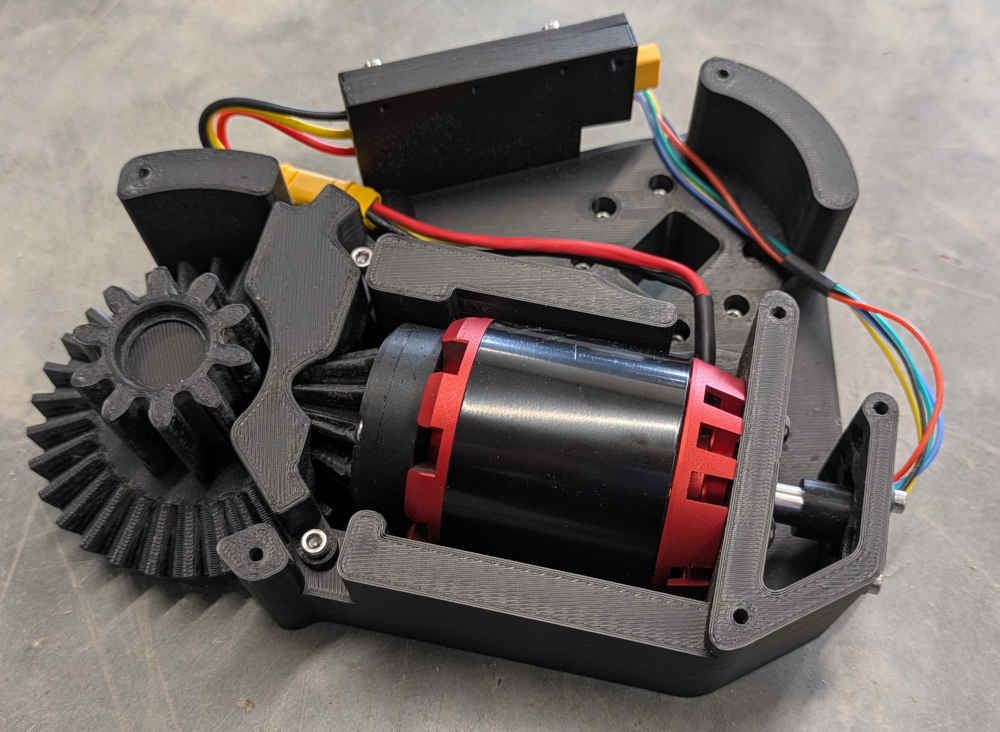
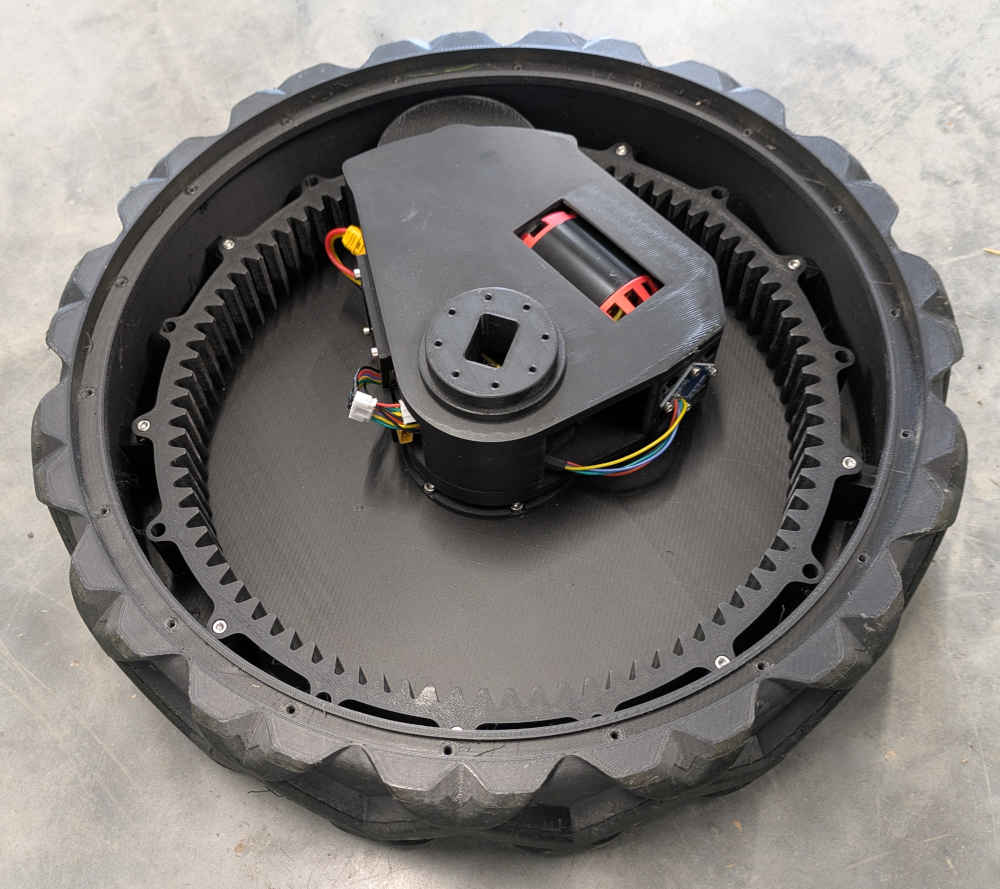
This dual-material strategy yields significant advantages. Firstly, it facilitates an extraordinarily fast turnaround on mechanical prototypes, enabling rapid design iteration. Much like agile methodologies in software development, we can quickly test, refine, and re-print components, accelerating our development cycles. Secondly, and perhaps more critically, it provides a pathway for manufacturing our robots in small to medium volumes without requiring substantial capital expenditure on tooling. This democratizes robot production, moving away from the need for massive factories and enabling a more agile, distributed manufacturing model that aligns with the specialized needs of agricultural technology.
For the critical aspect of motion, we have deliberately bypassed custom-designed, high-cost robotic actuators. Instead, our robots leverage commodity motion parts, drawing inspiration from high-volume industries. A prime example is our use of lightweight, high-performance brushless DC motors, widely adopted in drone technology. These motors offer an excellent power-to-weight ratio and are remarkably cost-effective due to their mass production. Paired with these are standard, off-the-shelf bearings and linear slides, chosen for their proven reliability and ready availability. As our designs mature, we systematically evolve from initial prototypes—where the focus is primarily on validating functionality—to more production-ready parts. This involves a rigorous process of identifying and mitigating potential failure modes, simplifying component geometries, reducing overall part count, and minimizing the number of fasteners required for assembly. This iterative refinement is fundamental to enhancing both reliability and manufacturability.
The electronics architecture follows a similar principle of strategic resource utilization. For precise motor control, we employ readily available motor driver Printed Circuit Boards (PCBs) based on cost-efficient microcontrollers (MCUs). These provide the necessary low-level control and feedback mechanisms. For the higher-level intelligence, our robots utilize powerful single-board computers, such as Raspberry Pis, integrated with the latest generation of edge AI chipsets. These compact yet powerful processors enable our robots to perform complex tasks like real-time visual analysis for crop and weed detection, autonomous navigation, and intelligent decision-making directly on the device, without constant reliance on cloud connectivity. This on-board processing capability is vital for operations in remote agricultural settings where network and mobile infrastructure may be limited.
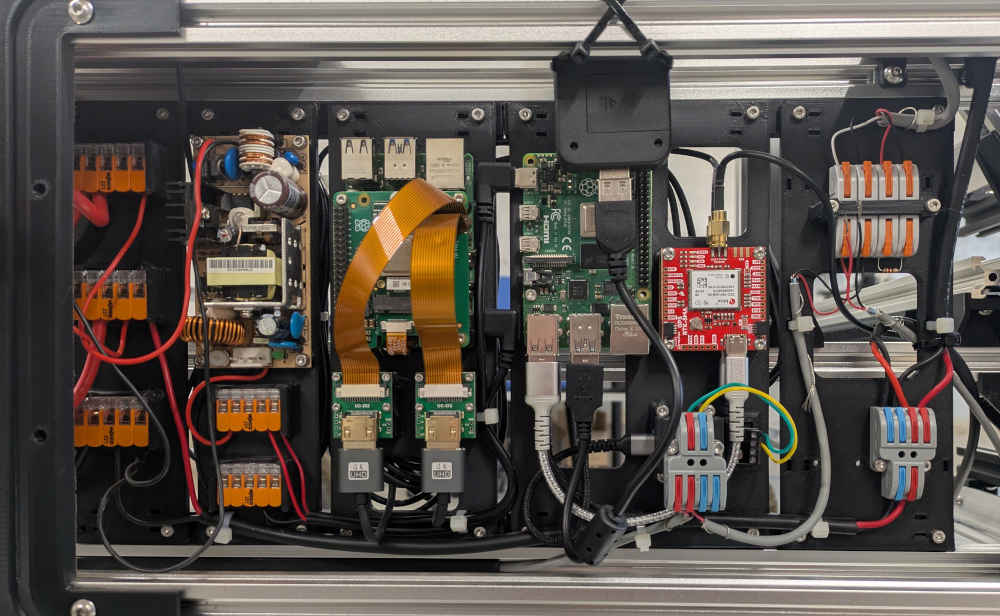
Finally, the ongoing advancements in battery technology play a pivotal role in the overall viability of our designs. The multi-decade continuous reduction in battery prices, coupled with improvements in energy density and lifespan, allows us to power our robots for extended periods, further enhancing their operational efficiency and reducing the total cost of ownership.
"We're building robust, cost-effective robots to make advanced farm automation genuinely accessible."
In essence, our approach is not merely about assembling cheap parts; it is about a thoughtful engineering strategy that combines the flexibility of additive manufacturing with the efficiency of mass-produced components. This holistic design philosophy enables Spring Agriculture to deliver performant, reliable, and economically accessible robots, marking a significant step forward in bringing advanced automation to the fields that feed our world.